A Comprehensive Approach to Addressing Stretch Cover Machine Fixing Difficulties
You know that stretch wrap makers are crucial for keeping efficiency in product packaging operations. However, concerns can develop that interrupt productivity. Understanding common troubles and carrying out preventative maintenance can substantially minimize downtime. And also, having well-trained drivers can make all the distinction in troubleshooting. What are the best approaches to ensure your machines run efficiently? Allow's explore the vital components of a detailed approach to tackle these repair work tests effectively.
Recognizing Usual Stretch Cover Maker Issues
When you count on stretch wrap makers for effective packaging, it's essential to identify common issues that can interfere with procedures - stretch wrap machine repair. One common problem is irregular tension, which can result in inadequate wrapping and jeopardized tons security. If you notice the film isn't sticking properly, look for worn-out rollers or incorrect setups
An additional concern you might deal with is film breakage, frequently triggered by wrong movie kind or equipment breakdowns. Regularly inspect the machine for signs of wear and tear to prevent this.
Additionally, watch on movie buildup or jams, which can halt production. Commonly, this happens due to imbalance or debris in the maker.
Finally, improper securing can result in lots splitting up during transit. Make sure your device is adjusted properly to maintain the integrity of your plans. By remaining cautious and addressing these problems immediately, you can facilitate smoother procedures.
The Importance of Routine Preventive Maintenance
Normal preventive upkeep is essential for maintaining your stretch cover machine running smoothly and efficiently. By consistently checking and servicing your devices, you can find potential issues before they rise right into costly repairs. This positive technique not just prolongs the lifespan of your equipment yet likewise ensures that it operates at peak performance.
You need to schedule routine inspections to tidy, oil, and replace used parts. Maintaining your device calibrated assists maintain optimal covering top quality, minimizes waste, and boosts productivity. Additionally, documenting upkeep tasks produces a reliable background that can educate future choices.
Don't forget the relevance of training your team on upkeep finest techniques. When everybody understands just how to look after the device, you reduce the risk of driver error resulting in failures. In other words, dedicating to normal precautionary maintenance is a clever financial investment that pays off in lowered downtime and improved performance in your procedures.
Repairing Methods for Quick Services
Effective repairing techniques can significantly decrease downtime when your stretch cover maker encounters concerns. Start by identifying the signs. Is the device not wrapping effectively or is it making unusual sounds? As soon as you have actually determined the problem, refer to the operator's manual for support on common problems and remedies.
Next, inspect the machine's setups and controls; occasionally, a simple change can solve the issue. Examine the movie tension and alignment, as incorrect setup can cause wrapping failures. Do not ignore electrical connections; loose or damaged cables can interrupt functionality.
If you're still encountering challenges, take into consideration running diagnostic examinations if your device has that capacity. File each action you take, as this can help in future troubleshooting and fixings. Lastly, don't be reluctant to seek advice from with a service technician if you can't deal with the concern swiftly. Effective fixing keeps your procedures running efficiently and reduces costly hold-ups.
Training Operators for Effective Device Usage
To assure your stretch wrap machine operates at peak performance, appropriate training for operators is essential. When drivers understand the equipment's performances, they can optimize its potential and lessen downtime.
Urge them to practice under supervision, attending to any type of inquiries or problems they may have. Regularly set up correspondence course can maintain their skills sharp and assist them adapt to any kind of updates or changes in innovation.
In addition, impart a culture of responsibility by equipping drivers to report issues or recommend renovations. This proactive method not just boosts their self-confidence yet also adds to the total performance of your operations. With trained drivers, you'll see less errors and boosted productivity, guaranteeing your stretch wrap device continues to be a beneficial possession.
Developing a Strong Interaction Network Between Teams
Trained operators can just execute at their finest when there's a strong communication channel between groups. Reliable communication eliminates misconceptions and guarantees every person's on the same page concerning machine operations and repair service requirements. Encourage normal check-ins and conferences to review concerns, share insights, and address problems.
Utilizing technology, like messaging apps or collective platforms, can boost real-time interaction, making it less complicated to report problems and share updates swiftly. Appointing clear roles and responsibilities cultivates accountability, enabling team members to connect to the appropriate individual when concerns develop.
In addition, developing an open setting where everybody really feels comfortable sharing feedback can result in cutting-edge remedies. By prioritizing communication, you're not just boosting device efficiency; you're also building a natural team that functions with each other perfectly. This joint spirit eventually causes quicker repair work and minimized downtime, benefiting the whole operation.
Purchasing Top Quality Substitute Components
When it concerns keeping your stretch wrap equipments, buying top quality replacement components is crucial for making sure dependable performance and decreasing downtime. Economical alternatives may seem tempting, however they often result in more considerable concerns down the line, costing you much more in repairs and lost performance. By picking high-quality components, you're not just dealing with a problem; you're enhancing the overall effectiveness of your devices.
Furthermore, top quality parts are typically manufactured to stricter criteria, which implies they'll fit far better and operate more dependably. This lowers the likelihood of unforeseen malfunctions, enabling your procedures to run efficiently. Furthermore, respectable suppliers commonly offer service warranties, giving you tranquility of mind in your investment.

Analyzing Performance Data for Continuous Improvement
To improve your stretch cover machine's performance, you need efficient data collection methods. By assessing performance metrics, you can determine locations for renovation and enhance effectiveness. Identifying these opportunities not just simplifies operations but additionally decreases downtime and fixing prices.
Data Collection Techniques
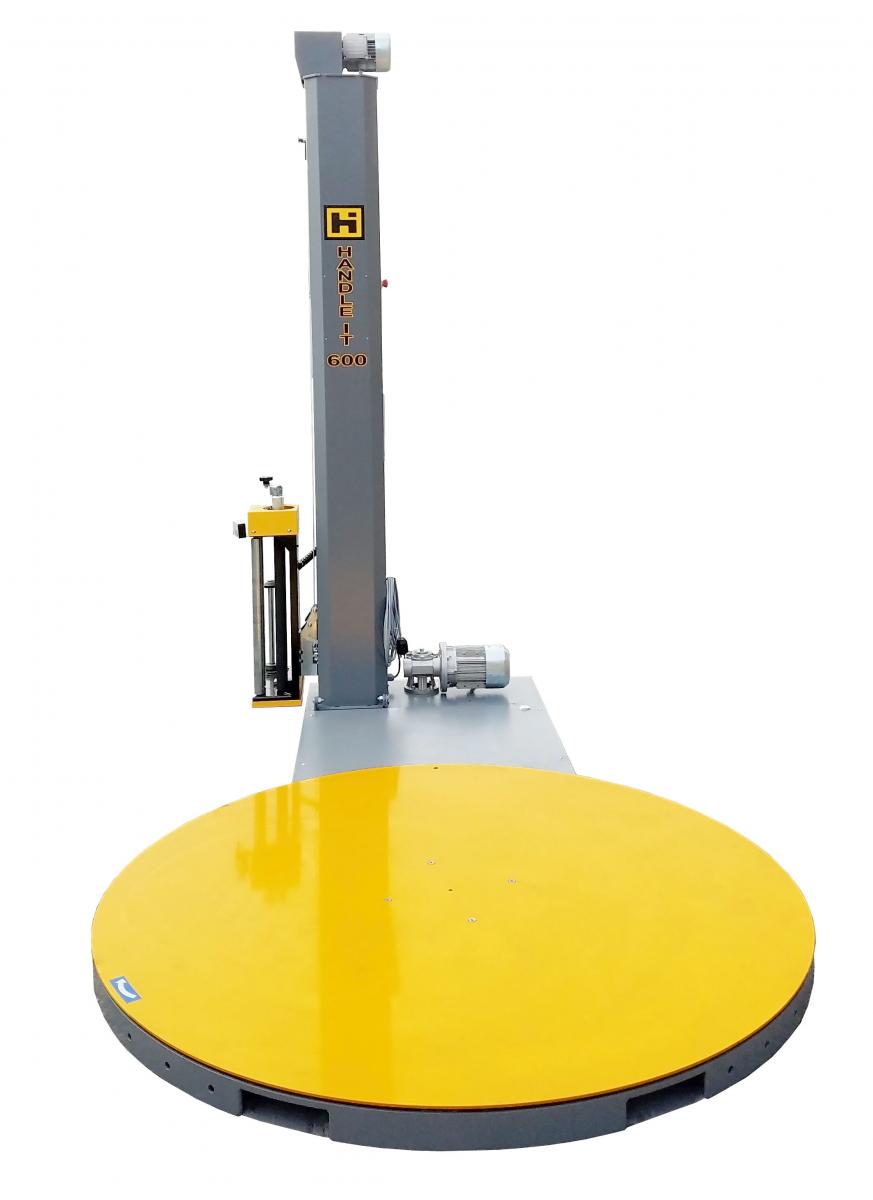
Efficiency Metrics Analysis
While assessing efficiency metrics, it's essential to concentrate on certain data factors that straight affect your stretch cover maker's performance. Start by tracking cycle times, as they disclose just how quickly your maker runs under typical problems. Screen downtime events to determine patterns or persisting concerns that may require resolving. Keep an eye on film usage, ensuring you're not losing material, which can impact prices and performance. Furthermore, examine output top quality by checking for incongruities in the covering procedure. By assessing these metrics on a regular basis, you can determine areas requiring attention and take positive measures. This constant assessment aids boost productivity, reduce expenses, and ultimately enhance your device's longevity, leading to a more reliable wrapping operation on the whole.
Identifying Renovation Opportunities
As you assess performance data, you can discover useful improvement chances that enhance your stretch wrap equipment's performance. Seek trends in downtime, cycle times, and wrap quality. By recognizing patterns, you'll see which areas need focus. For example, if frequent failures associate with certain operating problems, you can change procedures to alleviate these issues. Furthermore, contrast your information against sector benchmarks to determine your efficiency. Involve your group in discussions about the searchings for; their understandings can reveal sensible services. Carrying out minor adjustments based upon this analysis can lead to significant gains in productivity. Frequently taking another look at and updating your performance information will certainly assure constant improvement, maintaining your operations running smoothly and successfully.
Frequently Asked Questions
How Can I Tell if My Machine Requirements a Repair Work or Just Upkeep?
To tell if your equipment needs fixing or simply upkeep, listen for uncommon sounds, look for inconsistent performance, and inspect for visible wear. If problems linger after upkeep, it's most likely time for a repair service.

What Is the Typical Lifespan of a Stretch Cover Machine?
The average life-span of a stretch cover machine is generally five to 10 years, depending on use and upkeep. Normal care can extend its life, so keep an eye on efficiency and address concerns immediately.
Are There Details Brand Names Recognized for Better Reliability?
Yes, some brands are known for their integrity. You'll find that companies like Signode and Lantech usually get favorable evaluations - stretch wrap machine repair. Looking into user feedback can assist you select a trustworthy stretch cover maker for your requirements
What Are the Signs of Poor Operator Training?
If you discover frequent errors, inconsistent covering, or safety occurrences, those are signs of inadequate operator training. Lack of recognizing about machine features or failing to adhere to procedures can greatly impact effectiveness and security.
Just How Can I Locate a Qualified Technician for Fixes?
To locate a certified service official source technician for repair work, ask for referrals from sector peers, inspect on-line evaluations, and confirm accreditations. You may additionally think about speaking click this site to neighborhood tools distributors who commonly have trusted service technicians available.
Conclusion
To sum up, tackling stretch wrap maker repair obstacles requires an aggressive method. Don't fail to remember the significance of strong interaction in between teams and constant examination of maker outcome.